
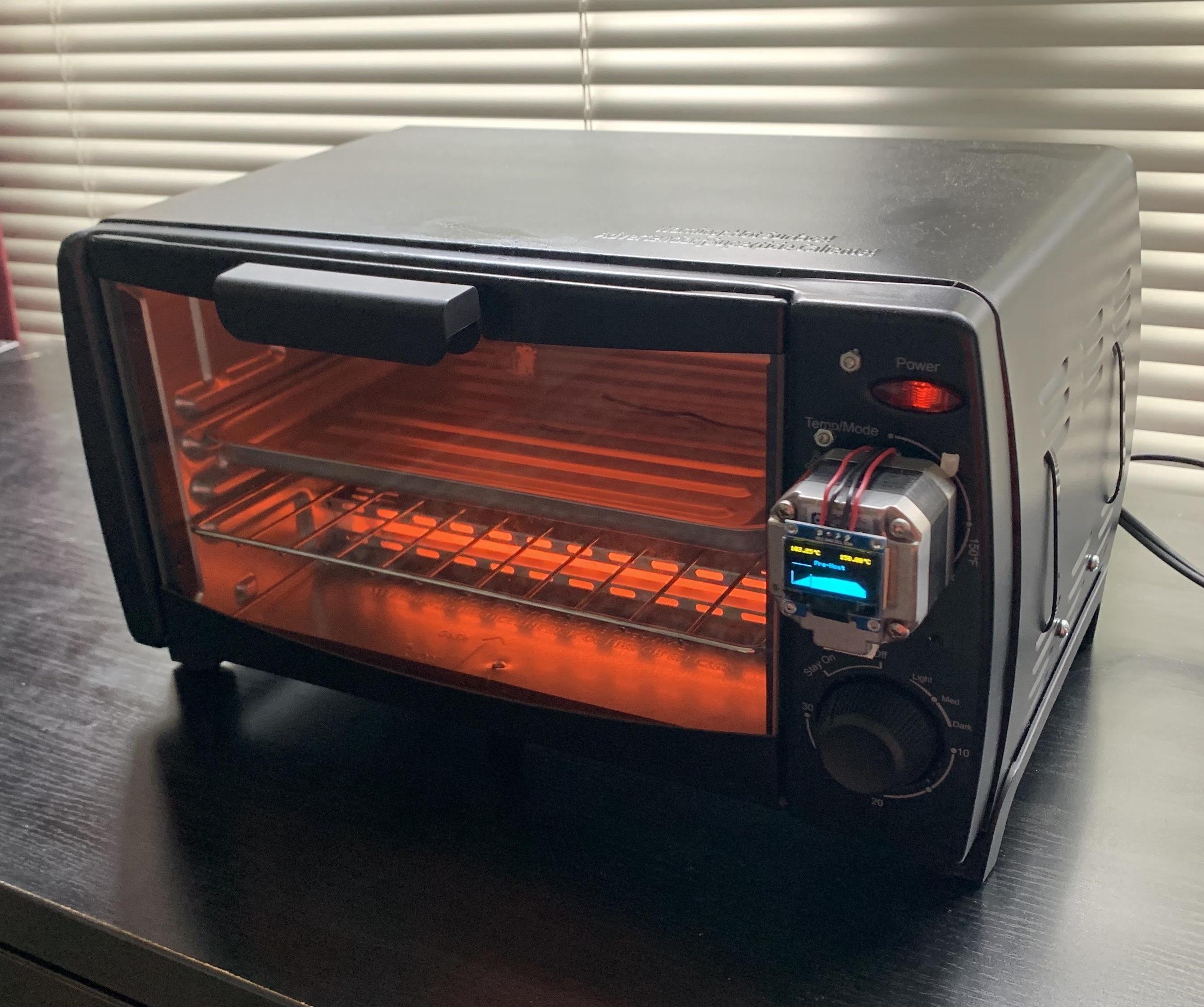
During the soldering process, the substrate and the component body are kept at a lower temperature, the soldering stress is low, and the components and the substrate will not be damaged. The laser beam is concentrated in a small area and within a short period of time through the optical system, so that the welded part forms a highly concentrated local heating zone. The laser beam reflow oven utilizes the excellent directivity and high power characteristics of the laser beam. Therefore, with the development of lead-free, the gas-phase reflow furnace has once again attracted people's interest, and is used for high-reliability and difficult-to-heat surface mount boards.Ģ) Reflow oven that locally heats the Circuit board However, the gas-phase reflow furnace has the advantages of accurate temperature control, heating media with different boiling points to meet different soldering temperatures of various products, high heat conversion efficiency, rapid heating, oxygen-free environment, uniform temperature throughout the PCB, and good soldering quality. The gas phase reflow furnace was used in the early 1970s, but due to the high cost of equipment and media, it was quickly replaced by other methods. Therefore, the infrared hot air stove also has a certain utilization rate in today's lead-free soldering. Due to the high soldering temperature of lead-free soldering, the reflow zone is required to increase thermal efficiency, so infrared heaters are added at the entrance of the hot blast stove and the bottom of the reflow zone, which not only solves the problems of high soldering temperature and speeds up the heating rate, but also saves energy. Infrared hot air reflow oven means that the heating source has both hot air and infrared rays. Therefore, the all-hot-air reflow oven has become the first choice for today's SMT reflow oven.
#Pcb reflow oven software#
In recent years, the hot-air reflow oven has adopted various measures in airflow design, equipment structure, materials, software and hardware configuration, etc. The hot air reflow oven has been used since the mid-1980s and has continued to this day. Components in shadow areas blocked by large components cannot easily reach the soldering temperature, resulting in a large temperature difference on the PCB, which is unfavorable for soldering. When infrared radiation radiates, dark-colored components absorb more heat than light-colored components, and infrared rays do not have the ability to penetrate. Infrared reflow ovens were popular in the 1980s. Due to the low thermal efficiency of this type of reflow oven, the uneven heating of the PCB surface and the special sensitivity to the thickness of the PCB, it was quickly replaced by other reflow ovens. The hot plate reflow oven was used in the early days of SMT. that heat the entire PCB laser reflow ovens and focused infrared reflow ovens are used for local heating of PCBs., Hot air flow reflow oven, etc. There are many types of reflow ovens, such as hot plate reflow ovens, infrared reflow ovens, hot air reflow ovens, infrared hot air reflow ovens, gas phase reflow ovens, etc. Lead-free reflow oven selection should be more cautious. In particular, the current lead-free soldering has the characteristics of high temperature, poor wettability, and small process window. The performance of the equipment has a direct impact on the quality of soldering. Soldering is one of the most critical processes in SMT. ˆšÂ It can increase the rate of tin feeding of pin components and then they will combine with the printed circuit board firmly.Reflow oven is the main soldering equipment in SMT assembly. If it happens to the connect between two spots of tin, it will cause short circuit. After that, the slag of tin will adhere on the printed circuit board. As the slag of tin will be formed when the liquid tin contacts with air. It is able to decrease the speed of oxidation of liquid tin in the bath. ˆšÂ Nowadays, some manufacturers also develop to put nitrogen in wave soldering oven. Because the rate of void decreases with oxidation. Because the nitrogen is a kind of inert gas which is hard to produce chemical compound. ˆšÂ It can decrease the oxidization in a certain. ˆšÂ It is able to make the surface tension of solder paste get smaller which is good for the components adhering to the PCB more easily.
#Pcb reflow oven how to#
After you have learned something about reflow oven, have you ever know how to make the reflow oven work better? Here are 3 benefits of putting nitrogen into reflow oven listed as following:
